Exploring the Unique Design Elements of the G. Rudolf Uebel "Cigar" Flute
- lindseymcchord
- May 5, 2023
- 5 min read
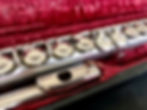
I recently had this Uebel “Cigar” flute come across my bench for some work and I just had to take a deep dive into the history of this really interesting instrument. I repair a lot of flutes of all makes and models but this one really surprised me because it is so solidly built and plays at a level of precision that rivals many modern flutes of today. If you’ve never seen or played a Uebel you’re not alone; they aren’t all that easy to find. Let’s dive into the history of this flute and go through some of the things that make it so special.

Built in 1967 by Gerhard Rudolf Uebel (1915-1991) in Wohlhausen, Germany, this particular flute was made with so many neat little design ideas. His family started making woodwind instruments in the 1870’s in East Germany and quite were successful at it. When his uncle F. Arthur Uebel passed away in 1963, Rudolf took over the flute production operations. Rudolf introduced various innovations and also used some unconventional materials such as, in this case, a body made entirely of aluminum.
The number on the body tells us the model number (#116), the year it was built (1967) and the serial number. Since this flute is owned by a client of mine I won’t reveal the serial number here. This flute is a unibody design made of thick aluminum.

There is no detachable footjoint like we typically see and the headjoint is unbelievably long with nearly no space for a traditional cork and cork assembly beyond the lip plate. The overall shape and size is more reminiscent of wooden instruments, and the tubing is the same thickness as a modern wooden flute. It is affectionately called the “cigar" flute due to the tapered ends and bulky body size.

It is a very well constructed flute with milled from a solid piece of aluminum. The mechanism is precise and very tightly placed. This makes for quick movement and silent action which is something many modern manufacturers still struggle to get right today. The interior of the bore is smooth and shiny and the tone holes are finished with the same degree of care. Upon closer inspection, what seemed at first to possibly be a somewhat clunky instrument actually is a highly precise, professional quality instrument.
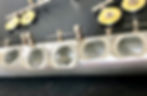
The tone holes are recessed into the body and are similar to those found on wooden flutes. Typically on modern metal flutes we see soldered or drawn tone holes with only a thin rim of metal making contact with the pad. In this case, there is a small raised rim to make contact with the pad and then a flat area around the tone hole making the key action feel very stable and solid. There are no ribs on this flute; instead the posts are set directly into the aluminum of the body. The posts are well set and show no sign of malfunction despite the age of the instrument.

The keys and headjoint are silver plated and the plating appears to be quite thick. I could see no sign at all of wear on them so initially I thought they were solid silver. The headjoint seems to be slightly more thinly plated than the keys, since it has some small areas of the base metal showing through on the tenon.
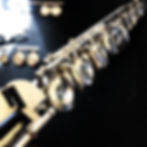
All of the main line keys are the same size, with relatively shallow key cups. We’re used to seeing several different sizes of tone holes and pad sizes on one flute but in this case the only tone holes that are small are C1 and trills. The shallow key cups seem particularly well suited to thinner (under 2mm) felt pads. Anything thicker than this and the pad protrusion becomes problematic.
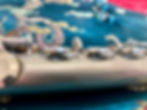
The key heights tend to be a little on the low side compared to some modern flutes, but this seems to work very well in this case. The keys are large and have a pleasant scoop shape to them making them very comfortable and free of distracting ridges. All of the keys are closed hole.

There are some unique characteristics to the key angles and placement. The thumb keys have a generous size and rounded square shape, making them quite comfortable and sliding from one key to the other is effortless.

The G# lever is quite low, presumably to make it easier to reach with those that have smaller hands and the lever itself is fairly wide.

The A# gizmo is a perfectly round little button that fits in perfectly with the shape of the other keys.

The trill levers are half-moon shaped and very slim, as is the G# arm.
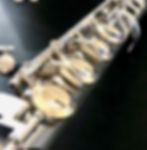
The D# C and C# keys are angled forward and not lined up in the typical way we might tend to set up a modern flute. The configuration is comfortable and feels natural. The rollers are a black plastic and are very well made; they fit tightly on the steels and have no play, and yet they roll beautifully.

The mechanism is held together using a variety of teeny tiny pivot screws and set screws. Instead of using pins to hold the left hand and right hand sections together, they are held in place using tiny screws.

I appreciated this because I’ve seen too many sad flutes come across my bench that have been damaged by previous technicians’ attempts to remove stuck pins. This design makes the whole process so much gentler. The screws that hold the key sections in place each have a small screw accompanying them on the posts that hold them in place and keep them from backing out. This allows for very precise adjustments to be made and also removes the issue of screws moving around over time or during shipping.
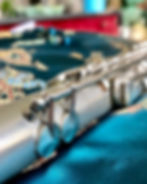
The headjoint is quite a bit longer than a typical flute headjoint.

This makes the entire instrument feel a bit unbalanced in the hands but with some time it begins to feel more natural. The length of the top of the headjoint beyond the lip plate is greatly reduced from what we see on a typical headjoint.

There is no cork assembly; in its place there is an aluminum crown that is fixed in place. I could see on this particular headjoint is looks like a previous technician had tried to remove it and caused a bit of damage. The crown has a hole in the center that extends nearly all the way to the cork plate, almost as though the intention was to take away as much weight from this area of the headjoint as possible.

The oval embouchure hole is cut fairly conservatively in size, with very slim overcuts and moderate undercuts. It is resistant and not particularly free blowing in general. The tonal quality is strong and clean however, balancing nicely between bright and dark.
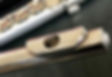
My client asked me if it would be possible to make an adapter to extend the length of the body so that it could be played using a modern headjoint. I went ahead and made one out of silver and it seems to work very well.
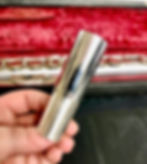
With the adapter and modern headjoint in place, the physical balance of the flute is much improved and the overall playing quality is much higher. When paired with my Lotus style headjoint for example, this flute is free blowing and colorful. Paired with my Dahlia style headjoint, this flute had some resistance keeping it from feeling too open, while still maintaining a flexible and fluid feel through the range of the instrument.
I really enjoyed having this Uebel in the shop and learning more about this really fascinating instrument. It was delightful to see the level of precision that was used to build this flute and it was wonderful to see all of the different ways Uebel worked around the common flute building issues. If you haven’t tried one of these I highly recommend you do if you come across one – it’s a tastefully made flute with a really beautiful sound quality.